Our special dry out and heat up technology is based on the use of Hotwork International High Velocity Burners operating on an excess air basis, which have been especially developed for the dry out and heat up of all types and sizes of furnaces/kiln/vessels and refractory lined components. The system permits a positive pressure assuring uniform temperatures in the vessel/piping components etc. Our system has been developed to ensure that precise temperature control of hot gas emissions generated by the high velocity burner can be regulated at all stages between 60°C and 1200°C, simultaneously eliminating hot-spots or stagnant areas within the vessel/furnace. The Hotwork International-Technology permits temperature uniformity of ± 3°C.
Pre-Heater / Tower
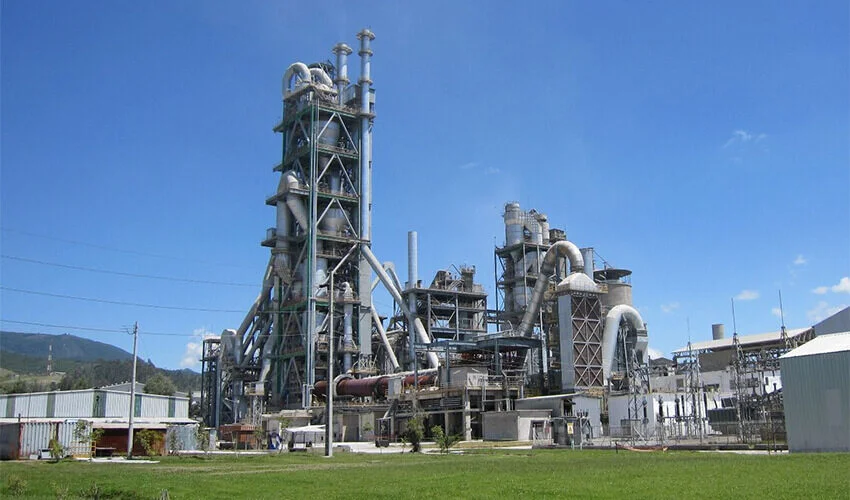
Newly commissioned cement pre-heater and calciner towers contain a huge amount of new refractory lining holding large amounts of water. Hotwork International offers refractory dry out to remove the moisture safe and effective. With over 35 years of experience, Hotwork International has the experience to do the engineering on burner installation points, hot gas flow and vent/stack position, maximizing the refractory lifetime.
- Complete units / greenfield after Maintenance
- partial after Maintenance Why Important?
- Improving campaign life time
- Prevent pre-mature refractory failure
- Prevent steam explosion and cracking

Modern refractory for the cement and mineral processing industry are designed for high efficiency, durability and easy installation. How ever they are vulnerable in newly installed units or after maintenance in green states. Applying the wrong way of initial heating and dry out leads to steam explosion and macro cracking reducing the over all refractory campaign life and premature refractory failure. Which may not be visible seen until the first cool-down when refracotry shrinks.
Under normal start-up conditions using the kiln burner, heat is introduced at the firing hood and drafts up the kiln. The cooler does what it is designed to do – it cools. Later on the refractory dryout happens in seconds when it is bathed in hot clinker. The Hotwork method applies precisely controlled heat which dries the curbs and bullnose, firing hood and nose ring. Dry-out and pre-heating can be done at the same time as the start-up.
Applying the Hotwork method, using high velocity burners to dry out refractory offers the most precise temperature control, exact to the specification of the refractory manufacturer. The Hotwork method utilizes precise controlled convective heat for an accelerated moisture removal. Our unique systems allows an accurate temperature control from ambient up to 1200°C (2200°F) with an incredible high turndown capability of 100:1.
Maintenance and Full Units dry-out:
Hotwork works on jobs including 1 to full unit dry out with 25 burners.
Fuel´s used:
Natural gas, propane or any gaseoues fuel as well as light oil, diesel, including the complete temporary piping for the fuel supply, offers a worry free solution.
Raw Mill:
A new facility is in need of temporary heat-supply, because there is no way to start a preheater without feed and heat is needed from a kiln to generate feed.