Modern design technology requires the installation of large amounts of expensive refractory for high temperature process. Newly installed refractory require a carefully controlled initial heating. If the initial heating is carried out to rapidly and or with local hot spot, then diffrent rates of expansion between adjoining refractory areas may occur, creating stresses which cause severe cracking or worth damages. Residual moisture may be converted to steam too quickly, resulting in a explosion. Both events will naturally have an impact to the efficiency and life time of the refractory. Most conventional process heat sources do not afford the close temperature control in the lower ranges (during which steaming will normally take place) and are less ideally suited to carry out the initial dry out or heat up. Moisture might drive into the refractory and is trapped, even so the refractory hot face may appear dried out.
Furnace Dry out / Heat up
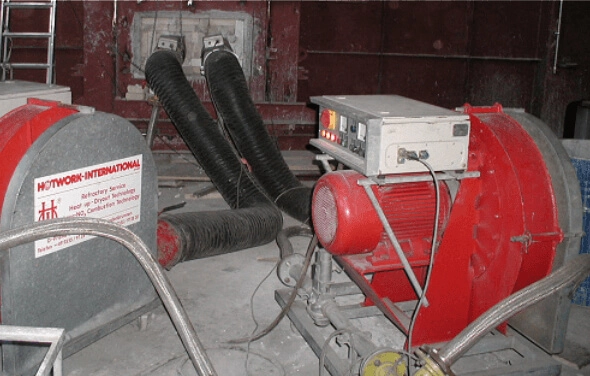
Proper heating of refractories is essential to avoid cracking or explosions. Conventional heating methods often fail to ensure even temperature distribution. The most effective solution is using a heat source that passes hot gases over the refractory surface, ensuring uniform temperature and complete moisture removal.
- Even temperature distribution
- Extend Refractory life
- Reduce risk of steam explosion
- Cost effective
- 365 days/year available
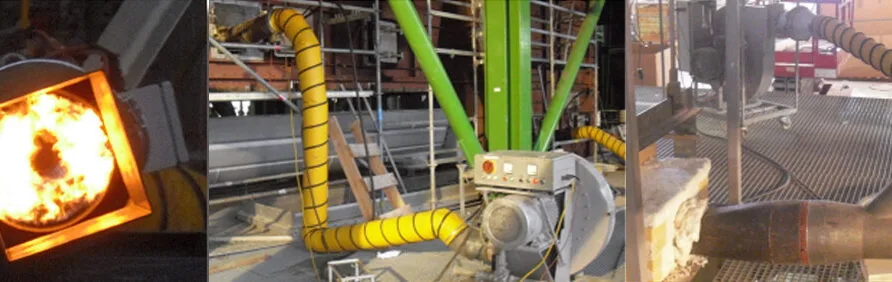