The Hotwork PERMANENT DRAIN system has been installed on various furnaces in the glass industry, such as tableware, flacons and special glasses for display, and fiber glass, to avoid defects called Zircon cords or cat scratches. Glass is being drained from the bottom of the Furnace, the Forehearth or the Working End. It is vital to ensure a slow-running, controllable glass drain. A funneling effect occurs If too much glass is removed and that would lead to the draining of hot glass from the upper areas instead of draining the colder and more viscous glass from the bottom. The Hotwork PERMANENT DRAIN provides exactly what is needed – a controllable drain system which can be operated at very low flow rates.
Permanent Drain for Special Glass
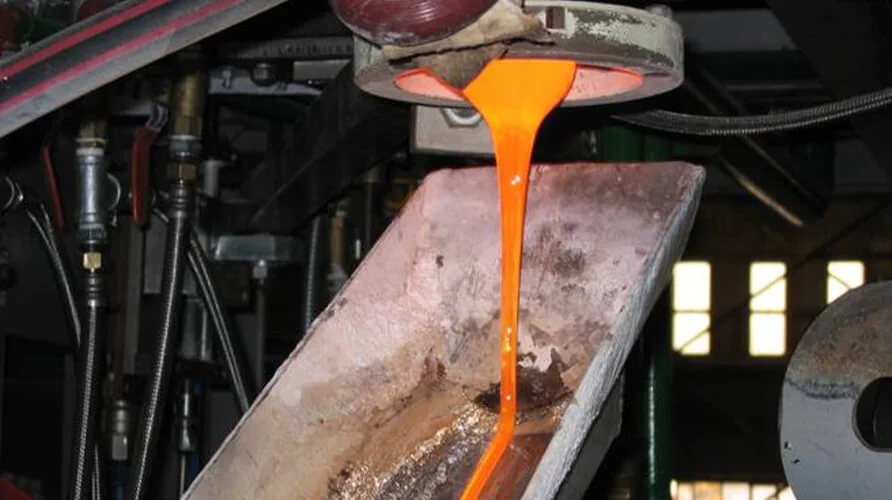
Experience a revolutionary solution for your drainage needs with our Permanent Drain service, specifically designed for special glass applications. Transform the way you manage drainage, ensuring longevity and optimal functionality for your unique glass installations.
- Precise Flow Control via PLC
- Easy to stop and restart drain
- Computer based bushing designing for specified temperatures and flow rates
- Bushing and Plunger made from platinum metals or special alloys for high temperature application 1700°C+
- Small size water cooled high current transformers with thyristor control
- Exchangeable mouth pieces even during operation
- Precise plunger positioning either manual or automatic SPC process control with OP systems
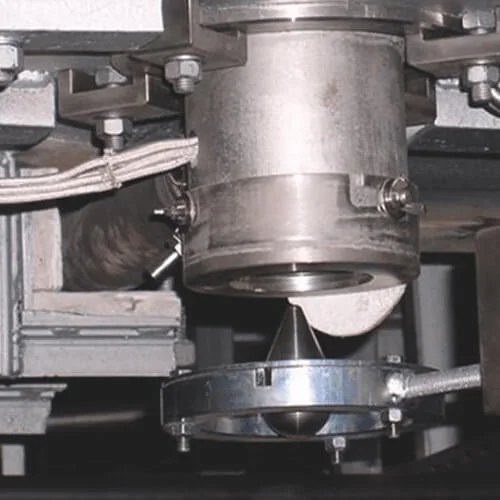


The Hotwork PERMANENT DRAIN system comprises a special electrical heated Platin Flow Bushing with water cooling heated via Transformer and Thyristor Control, a Control Plunger to adjust the flow a specially designed channel block together with an PLC control enclosure and Cooling Water station. The channel block features a drain hole at the bottom of a specially shaped well. The block itself is normally fused cast AZS to facilitate operation of the electrical heating system. The PERMANENT DRAIN itself consists of a high temperature resistant alloy which acts as an outlet nozzle. This is placed up against the underside of the outlet hole on the channel block. A simple ceramic holder assembly is used to keep the metal plate in position and provide electrical insulation. The temperature of the outlet nozzle is measured by a thermocouple. The electrical heating system comprises a small transformer with a thyristor unit to provide step less voltage variation. A temperature controller is used to maintain a constant temperature at the outlet nozzle, which results in a constant flow velocity of the glass. Adjustment of this temperature gives a change in the amount of glass being drained. It is imperative that the glass is drained slowly in a controlled manner. The amount of glass to be drained can be adjusted via the PLC Control, however in same cases the outlet nozzle can be changed to increase or decrease the glass flow amount. In most cases, the operating mode is continuous. However, discontinuous operation is also possible, as it is easy to stop and start the drain. Experience has shown that a daily drain of 500 to 1300kg per line is sufficient to ensure a good glass quality. The electrical power consumption will usually be between 1.0 and 2.5kW. Optional the drain block can be installed without the drain equipment. It is possible to install drain equipment and activate the system at a later stage.
Under some circumstances it is possible to install the Hotwork PERMANENT DEAIN on an existing Furnace/Working End/Forehearth with no special channel block by drilling the required profile from outside of the forehearth.