A bubbling system creates a controlled disturbance in the glass melt. Air or other gases are blown through special bubbler nozzles into the furnace. Depending on the design, mulitple or large bubbles rising from the bottom installation to the glass surface, where the bubbles exhaust the gas into the furnace atmosphere.
Bubbling
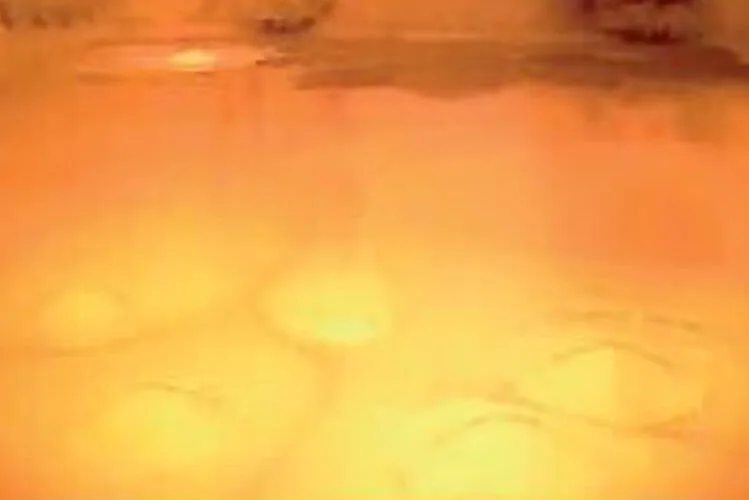
Discover a revolutionary approach to liquid processing with our cutting-edge Bubbler service. Designed to redefine industry standards, this innovative solution promises efficiency and versatility.
- Increased bottom temperate
- Reduced fuel consumption up to 5%
- Reduced Furnace Temperatures
- Improvied homogeneity
- Quicker colour change
- Increased production


These bubbles bringing cooler glass from the bottom of the furnace towards the surface, where it can absorb the heat from the flame, thus avoiding excessive crown temperatures to bring heat to the furnace bottom. The bursting bubbles on the glass surface also create an effective barrier that prevents unmelted batch from moving forward. Thus producing a physical barrier to the batch/ foam blanket. Benefits of bubbling are not only decreased fuel consumption and reduced firing temperature but also an increase of production capacity and quality of the product due to the improved homogenity. The improved glass flow in the furnace help to eleminate cords. The System has major advantages for the melting of coloured glass as it reduced product loss due to stone inclusions.
Technology Available:
Fiberglass
Container Glass / Forehearth
Float Glass
Special Glass, Crystal etc
Our Bubbler Tubes can be made off:
Ceramic (Operating Temp. 1950°C)
Water Cooled
Platinum or Platinum Coated
Inconel
Our references :
Over 60 Installations worldwide
Over 75 Power Controls worldwide